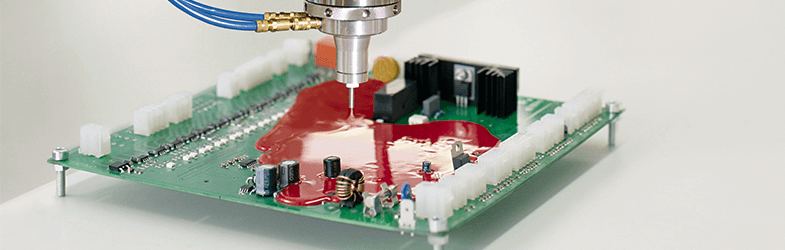
Resine bicomponenti da colata per electrocasting
Il Gruppo RAMPF è formato, tra le altre, dalle aziende Rampf Production Systems e Rampf Polymer Solutions.
Rampf Production Systems progetta e produce impianti per la miscelazione e il dosaggio di resine bicomponenti. Siamo in grado di fornire soluzione tecnologiche altamente avanzate e complete linee di automazione e movimentazione pezzi e non solo le tecnologie e i sistemi di dosaggio.
Per quanto riguarda Rampf Polymer Solutions, uno dei core business dell’azienda è la produzione di resine poliuretaniche, siliconiche ed epossidiche. Alcune di queste, ossia le resine per l’incapsulamento di componenti elettrici ed elettronici, hanno lo scopo di offrire protezione totale nei confronti di qualsiasi fattore che possa influenzare le prestazioni di queste stesse componenti. Sono infatti molte le possibili cause di malfunzionamento di questa componentistica, dall’umidità alla polvere fino a stress termici, chimici o meccanici.
Le resine da electrocasting sono fondamentali per lo sviluppo di numerosi settori industriali: automotive, energia, automazione, elettrodomestici sono tutti settori fortemente indirizzati dagli sviluppi nelle tecnologie di immagazzinamento e trasferimento di elettricità.
Le resine per l’incapsulamento mono o bicomponenti aumentano l’affidabilità e le performance della componentistica su cui sono applicate, rendendola maggiormente efficiente dal punto di vista economico e di più lunga durata.
Rampf Polymer Solutions offre un ampissimo portfolio di prodotti da utilizzare come resine per l’incapsulamento in modo da poter soddisfare le richieste di qualsiasi cliente. Inoltre, il laboratorio di R&D è sempre al lavoro per sviluppare nuove soluzioni che soddisfino le richieste dei nostri clienti.
Le resine di Rampf Polymer Solutions, utilizzate dai fornitori leader dei settori automotive e della componentistica elettronica sono certificate e listate UL94, RTI, OBJS2, e altre.
Caratteristiche delle resine per l'incapsulamento elettronico
Proprio questa capacità di confrontarsi con le necessità del cliente e creare una resina fatta su misura per la sua applicazione rende molto importante capire quali sono le caratteristiche che le resine da electrocasting devono rispettare. Vediamo insieme quelle più importanti:
Resistenza Termica e Indice della Temperatura Relativa (RTI)
La resistenza termica descrive l’invecchiamento dei materiali sotto l’influenza di una certa temperatura per un prolungato periodo di tempo. L’Indice della Temperatura Relativa (RTI, Relative Temperature Index) secondo lo standard UL 746 B è una misura dell’invecchiamento termico dei polimeri.
La resistenza termica di un materiale può essere determinata misurando il cambiamento nelle sue proprietà meccaniche ed elettroniche in relazione a un livello predeterminato. Le principali proprietà testate sono la forza dielettrica e la forza di tensione.
Per conoscere il RTI di un materiale dei campioni sono invecchiati ad almeno quattro temperature diverse, tutte superiori al RTI previsto (per un massimo di diecimila ore). Si raggiunge il RTI quando le caratteristiche fisiche (elettriche o meccaniche) calano del 50% rispetto al loro valore iniziale.
L’RTI dovrebbe essere misurato dopo aver dispensato il materiale sul prodotto, essendo importante l’analisi delle interazioni chimico-fisiche tra i componenti di un sistema durante la produzione e l’utilizzo.
Sono state formulate cinque classi di isolazione termica: classe A fino a 105°C, classe E fino a 120°C, classe B fino a 130°C, classe F fino a 155°C e classe H fino a 180°C.
Conducibilità Termica
Le resine bicomponenti, come tutti i materiali, hanno l’abilità di trasportare energia sotto forma di calore. La velocità a cui questo calore si diffonde nel materiale ne determina la conducibilità termica.
Poter condurre rapidamente il calore è importante nelle resine per l’incapsulamento di componenti elettriche, dovendo allontanare dal prodotto il calore causato dalla dissipazione di energia elettrica e proteggerlo da possibili stress meccanici.
Nelle resine poliuretaniche, siliconiche ed epossidiche vengono inseriti dei filler (cariche) minerali non metallici per aumentare la conducibilità termica della resina (in modo da poter dissipare calore mentre il prodotto sta lavorando) mantenendo l’isolazione elettrica.
Aria e gas hanno un valore di conducibilità di 0,1 W/m*K, i metalli di 400 W/m*K (non sono una buona scelta perché costosi e conduttori di elettricità), le resine per l’incapsulamento di Rampf Polymer Solutions hanno normalmente un valore tra 0,2 e 0,3 W/m*K senza aggiunta di filler e tra 0,8 e 1,1 W/m*K se modificate con l’utilizzo dei suddetti filler (potendo arrivare fino a un massimo di 2 W/m*K con dei particolari processi).
Temperatura di Transizione Vetrosa (Tg, Glass Transition Temperature)
È la temperatura a cui le resine da electrocasting passano da una condizione vetrosa, in cui sono dure e per niente elastiche, a una in cui sono più morbide ed elastiche. Questo passaggio porta la resina da incapsulamento a cambiare alcune delle proprie caratteristiche fisiche come il coefficiente di espansione termica, la costante dielettrica e la dissipazione dielettrica.
In alcuni casi questa temperatura può essere inferiore alla temperatura ambientale, se il prodotto necessità di una resina da colata che abbia costantemente caratteristiche di morbidezza ed elasticità. In caso contrario si cerca di avere un materiale con una Tg nettamente più alta delle temperature a cui il pezzo verrà a trovarsi in fase di lavoro, in modo da essere sicuri che la resina mantenga le caratteristiche che la contraddistinguono.
Coefficiente di Espansione Termica (CTE, Coefficient of Thermal Expansion)
Questo coefficiente, che è una costante propria di ogni materiale, indica la variazione in volume o in lunghezza di un materiale all’aumentare di un grado della temperatura. Il coefficiente di espansione termica va considerato nell’elaborazione del design del prodotto da resinare e nel caso vengano deposte due resine diverse con CTE non uguali.
L’uso di filler può diminuire il valore del coefficiente di espansione termica.
Temperatura di inflessione per calore (HDT, Heat Deflection Temperature)
Il valore di questa temperatura, specifico per ogni resina bicomponente, si ricava portando il materiale a diverse temperature sempre più alte dopo averlo sottoposto a un carico con un peso predeterminato. La temperatura a cui la resina da electrocasting inizia a deformarsi è la sua specifica HDT.
Resistenza allo Shock Termico
Per capire la resistenza delle resine da electrocasting alla temperatura, diverse resine con diversi CTE vengono portate a temperature tra i -60° e i -40°C, alzando poi la temperatura tra i 125° e i 160° C. I possibili problemi riscontrabili dopo questo test sono: la rottura dei componenti, la presenza di crepe sulla superficie della resina da colata e la delaminazione (separazione) tra la resina e il prodotto o i suoi componenti.
Per cautelarsi da questi rischi la soluzione è lavorare con un materiale rigido (con una temperatura di transizione vetrosa alta) e con un coefficiente di espansione termica basso in modo che la resina bicomponente sia stabile nel range di temperatura a cui è sottoposto, oppure di lavorare con una resina da electrocasting così morbida da poter aver un CTE alto senza stressare il pezzo.
Resistenza Chimica
Per valutare la resistenza chimica del prodotto dopo che questo è stato incapsulato attraverso il sistema di resinatura questo è immerso per una settimana in etanolo a temperatura ambiente. Dopo il test vengono valutate le difformità del prodotto rispetto alle sue caratteristiche precedenti all’immersione. Sono analizzate principalmente:
- il valore di durezza della resina da colata (normalmente in Shore D)
- l’aumento di volume e di peso in percentuale, per capire quanto etanolo è stato assorbito
- HDT (Temperatura di Inflessione per Calore)
Resistenza al Fuoco
Le caratteristiche di auto estinzione delle fiamme sono raggiunte tramite l’inserimento di cariche e/o additivi. Lo standard principale è l’UL 94, in cui i materiali sono classificati come V0, V1 e V2 in base alla reazione ottenuta dopo essere stati sottoposti a una fiamma di una determinata temperatura in una posizione verticale per due cicli da dieci secondi. Per stabilire la classificazione si misura per quanto tempo il campione rimane acceso dopo che la fiamma è stata spenta e se parte di esso gocciola e, così facendo, dà fuoco a un batuffolo di cotone posto sotto al campione stesso. Più il campione di resina è sottile, più è difficile che possa passare il test.
Fonte di Accensione Elettrica
Viene testata l’infiammabilità di un campione attraverso due test in cui sono stabiliti l’indice di infiammabilità da filo incandescente GWFI (Glow Wire Flammability Index) e la temperatura di accensione da filo incandescente GWIT (Glow Wire Ignition Temperature).
Per il GWFI il campione viene pretrattato per 48 ore a 23°C con il 50% di umidità e poi viene messo a contatto per 30 sec con un filo incandescente, si parte con 550°C e si sale di 50°C alla volta fino ad arrivare a 950°C.
Per passare il test tre campioni di fila devono: estinguere le fiamme entro 30 sec dalla rimozione del filo incandescente e non gocciolare dando fuoco a un pezzo di carta posto sotto al campione.
Per verificare la GWIT il campione viene pretrattato per 48 ore a 23°C con il 50% di umidità e poi messo a contatto per 30 sec con un filo incandescente, si parte da 500°C e si sale di 50°C alla volta fino ad arrivare a 950°C.
Se il campione messo a contatto con il filo incandescente non prende fuoco per più di 5 sec e non gocciola si passa a testare la temperatura più alta. La GWIT è di 25°C più alta della temperatura massima in cui il test è stato superato.
Come funziona il sistema di resinatura
Le resine (sia poliuretaniche, che siliconiche e anche epossidiche) sono generalmente formate da due componenti che reagiscono una volta miscelati insieme, indurendosi in pochi minuti fino a formare una resina solida e con le caratteristiche richieste dall’applicazione voluta dal cliente.
I sistemi di resinatura di Rampf Production Systems sono affidabilissimi e molto precisi, grazie all’utilizzo di pompe di dosaggio volumetriche che utilizzano un sistema a ingranaggi. Inoltre per essere costantemente certi della precisione dell’erogazione di entrambi i componenti che andranno a formare la resina dopo la miscelazione, fondamentale per ottenere un prodotto con le specifiche caratteristiche richieste, forniamo anche dei flussimetri che in ogni momento analizzano il lavoro delle pompe di dosaggio nella linea che porta il materiale alla testa di miscelazione e avvertono il produttore di eventuali modificazione nel livello attraverso allarmi specifici mostrati nella HMI (Human Machine Interface).
Qui sotto possiamo vedere un'immagine che illustra i passaggi che portano il materiale dai fusti alla testa di miscelazione.
- Stazione di trasferimento (1-2) La preparazione del materiale inizia nei fusti forniti da Rampf Polymer Solutions: il componente A (poliolo) viene generalmente mescolato a intervalli, diversamente dal componente B (isocianato) che non necessita di particolari trattamenti meccanici. L’unico accorgimento necessario per l’isocianato è la disidratazione dell’aria in ingresso al barile in fase di pompaggio.
- Preparazione del materiale (3-4) Dai fusti i due componenti vengono pompati automaticamente fino ai serbatoi di preparazione del materiale (daytank), che generalmente sono termoregolati per garantire stabilità di processo. Nei daytank avviene il cuore della preparazione in quanto i componenti vengono agitati (soprattutto il comp. A), ricircolati lungo la linea di alimentazione del materiale e termoregolati. In alcuni casi va anche applicato un processo di degasaggio a strato sottile (thin-film degassing) che priva il materiale della presenza di bolle d’aria che potrebbero inficiare il sistema di resinatura. I sistemi di resinatura brevettati di Rampf Production Systems permettono attraverso sistemi completamente automatici di ottenere una resinatura di alta qualità e sempre costante nel tempo.
- Dosaggio e miscelazione (6-7) Le pompe di dosaggio volumetriche a ingranaggi prelevano il materiale dalla linea di ricircolo per portarlo fino alla testa di miscelazione che può essere sia dinamica che statica, in base alle caratteristiche del materiale. Bisogna essere molto precisi nel dosaggio di questi componenti in quanto il rapporto di miscela tra di essi modifica alcune caratteristiche chimico-fisiche del polimero bicomponente.
La dispensazione di queste resine da colata può essere svolta sottovuoto per evitare la presenza di gas che potrebbero causare rotture durante i test di shock termico. Inoltre, l’incapsulamento sottovuoto è utile anche per prodotti con un design e una geometria che rischiano di favorire la creazione di bolle d’aria e per resine trasparenti. Il materiale dispensato sottovuoto risulterà infatti più omogeneo e meno poroso, con delle caratteristiche di flusso e impregnazione ottimizzate e avrà inoltre caratteristiche meccaniche ed elettriche migliori.
Per ottenere il miglior processo possibile alcuni parametri vanno ottimizzati:
- Temperatura del prodotto: influenza la viscosità della resina, importante per il flusso del materiale, e la reattività del sistema, che raddoppia/si dimezza al crescere/decrescere di 10°C della temperatura.
- Quantità di resina erogata e numero di shot: in questo modo si possono ottenere il giusto numero di layer per la resinatura dei componenti dell’articolo incapsulato.
- Pretrattamento delle parti: devono essere pulite da grassi, oli, polvere e umidità per favorire l’aderenza della resina e spesso vengono riscaldante per ridurre il restringimento, migliorare la fluidità della resina e avere un tempo di reazione minore.
- Hardening, curing e post-curing: sono le fasi in cui i componenti della resina da electrocasting reagiscono, facendola passare da una densità tipo gel a un solido, completando il processo e raggiungendo le sue caratteristiche definitive. Le resine da colata bicomponenti possono indurirsi anche a temperatura ambiente ma per raggiungere determinate proprietà fisiche bisogna portare il materiale sopra alla sua Tg (temperatura di transizione vetrosa).
Il tempo di curing dipende da molti fattori: la formulazione della resina da colata, i parametri di processo della miscelazione e dispensazione , il volume della resina dispensata, la temperatura e la geometria del prodotto prima del processo di resinatura e la temperatura del processo di curing. I parametri di riempimento e di curing degli articoli vanno adattati caso per caso.
Le resine da colata del gruppo Rampf
RAMPF POLYMER SOLUTIONS
Rampf Polymer Solutions non è solo una delle compagnie che compongono il Gruppo RAMPF, ma è il nucleo da cui tutto il gruppo ha incominciato la sua espansione oltre 40 anni fa.
Questa lunga esperienza come azienda chimica fornitrice di prodotti per l’isolamento di componenti di vari prodotti rende Rampf Polymer Solutions un’azienda forte e affidabile, con molte reference presso i principali OEM.
RAMPF PRODUCTION SYSTEMS
Rampf Production Systems è la compagnia del Gruppo RAMPF che produce i sistemi di miscelazione e dosaggio delle resine bicomponenti. I vantaggi di affidarsi a Rampf Production Systems sono molteplici, innanzitutto una delle caratteristiche che rende l’azienda unica è la capacità di produrre complete linee di produzione e automazione di processo: in un solo sistema possiamo offrire soluzioni di pretrattamento degli articoli, resinatura, di post trattamento dei pezzi attraverso forni o altri sistemi di riscaldamento delle parti, e anche di caricamento e scarico (con imballaggio se necessario) degli articoli.
Per ulteriori informazioni su ciò che avete letto non esitate a contattarci ai recapiti sottostanti.
RAMPF #discoverthefuture